"Airbow - An Anthropomimetic Elbow with Dual Pneumatic Actuators" was my Master thesis work and my first attempt at hardware electronics prototyping and programming with Arduino. The purpose of the thesis was to explore soft robotics as a way of making cognitive robots for embodied cognive science research. Cognitive science has in recent years realized the importance of embodiment for cognition. Related to embodied cognition is morphological computation. It is the claim that the body morphology can perform computational services. For example, the act of walking is a hard problem for traditional robots with hard bodies and motors as actuators, it requires huge computational power to walk on two legs in an unpredictable real world scenario. Then in 1990 Tad McGeer created the Passive Dynamic Walker. It's a machine that is able to walk very much like a human without any computation or actuators. It has roughly the morphology of a human skeleton and the legs move by passively shifting the body weight from one leg to the other, like pendulums. You can check out a passive dynamic walker made at Cornell University here. This means that bipedal walking that proved so difficult for traditional cognitive robots actually requires very little computation with the correct body morphology. With the Airbow I wanted to explore how difficult it would be to control the flexion and extension of a robotic arm that resembled the human morphology as closely as possible with 3D-printed skeleton, soft actuators (McKibben air muscles), elastic ligaments and tendons and evaluate the usefullness of this approach to cognitive robotics.
My conclusion was that the body is not only soft, but wet. It uses fluids to lubricate the joints and lower friction, which was my main problem. The elbow joint is also enclosed in skin, fat and connective tissue which would help greatly with the stability and durability of the prototype. However, I believe that it is inevitable that cognitive robotics must start making robots that have more similar body morphology to the cognitive agent that they are modelling.
Below are photos of my process that I documented on Instagram.
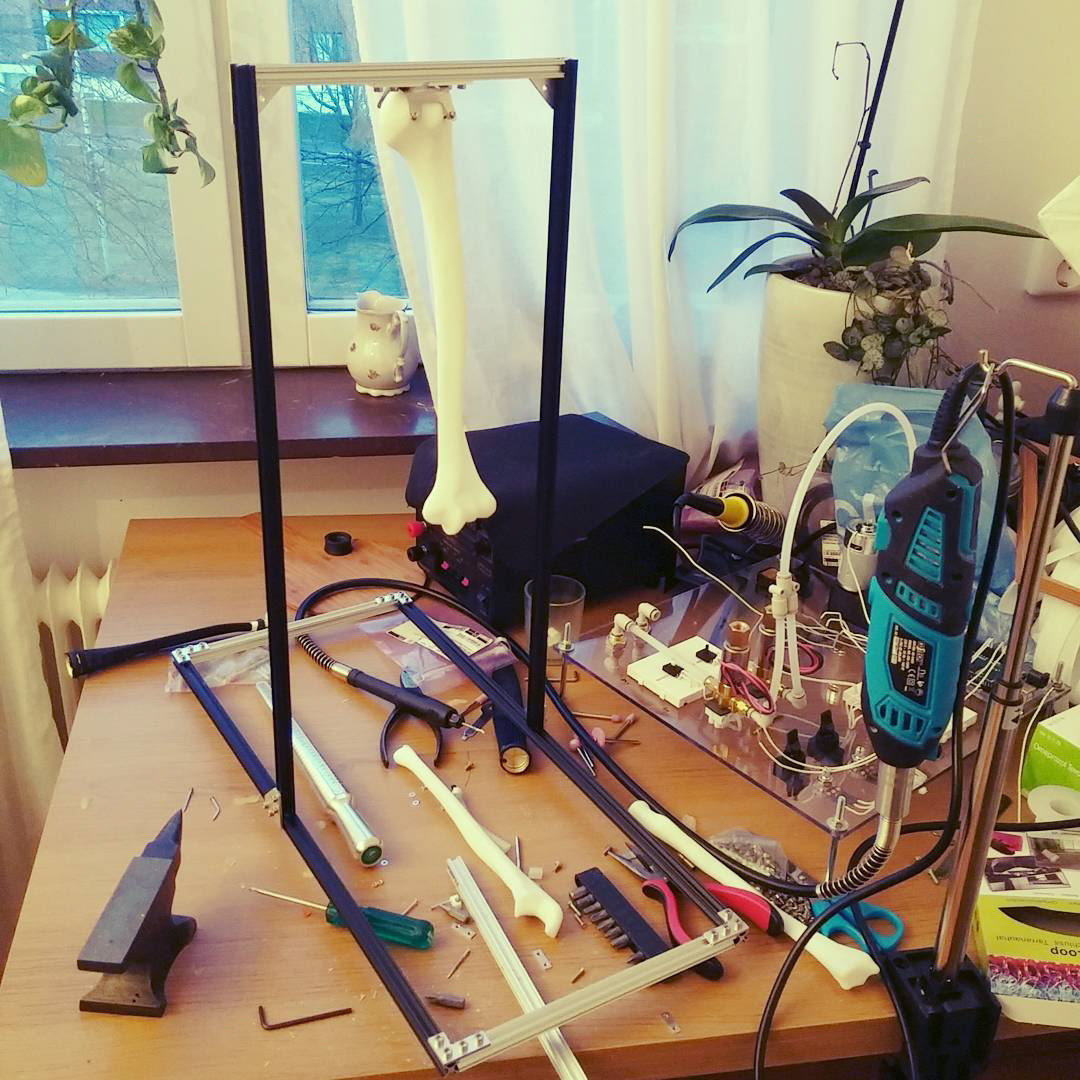
Attaching the 3D-printed humerus to the metal frame was difficult. Luckily I had just picked apart my broken laptop and found a metal piece that sat over my CPU that was perfect for the job.
How I made the McKibben air muscles.
Showing the first version of the angle sensor with some nice tunes from Kill The Noise in the background.
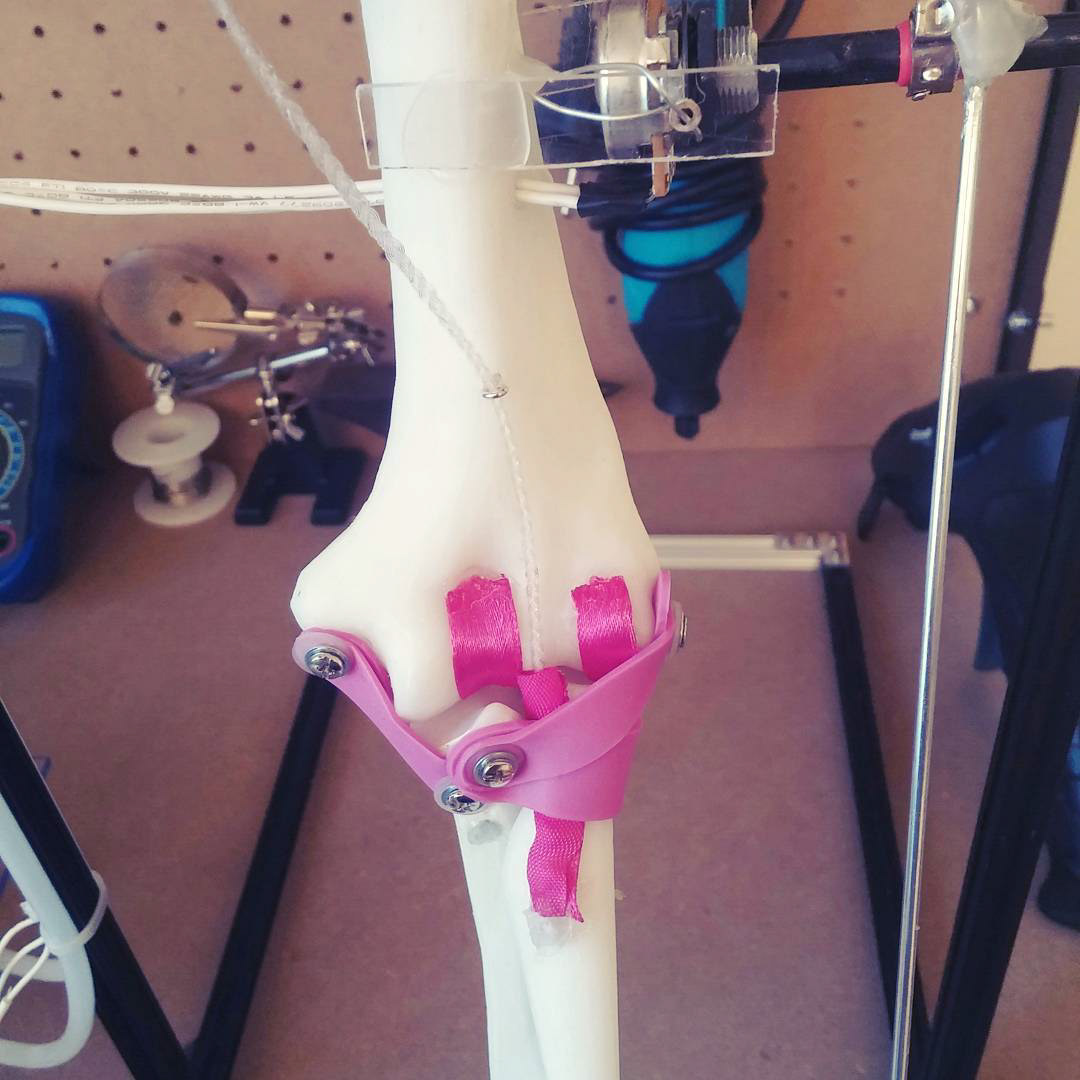
The ligaments were made from a silicone pot holder, the tendons were braided fishing line and I glued satin ribbons to the articulating parts of the joint to lower the friction like cartilage.
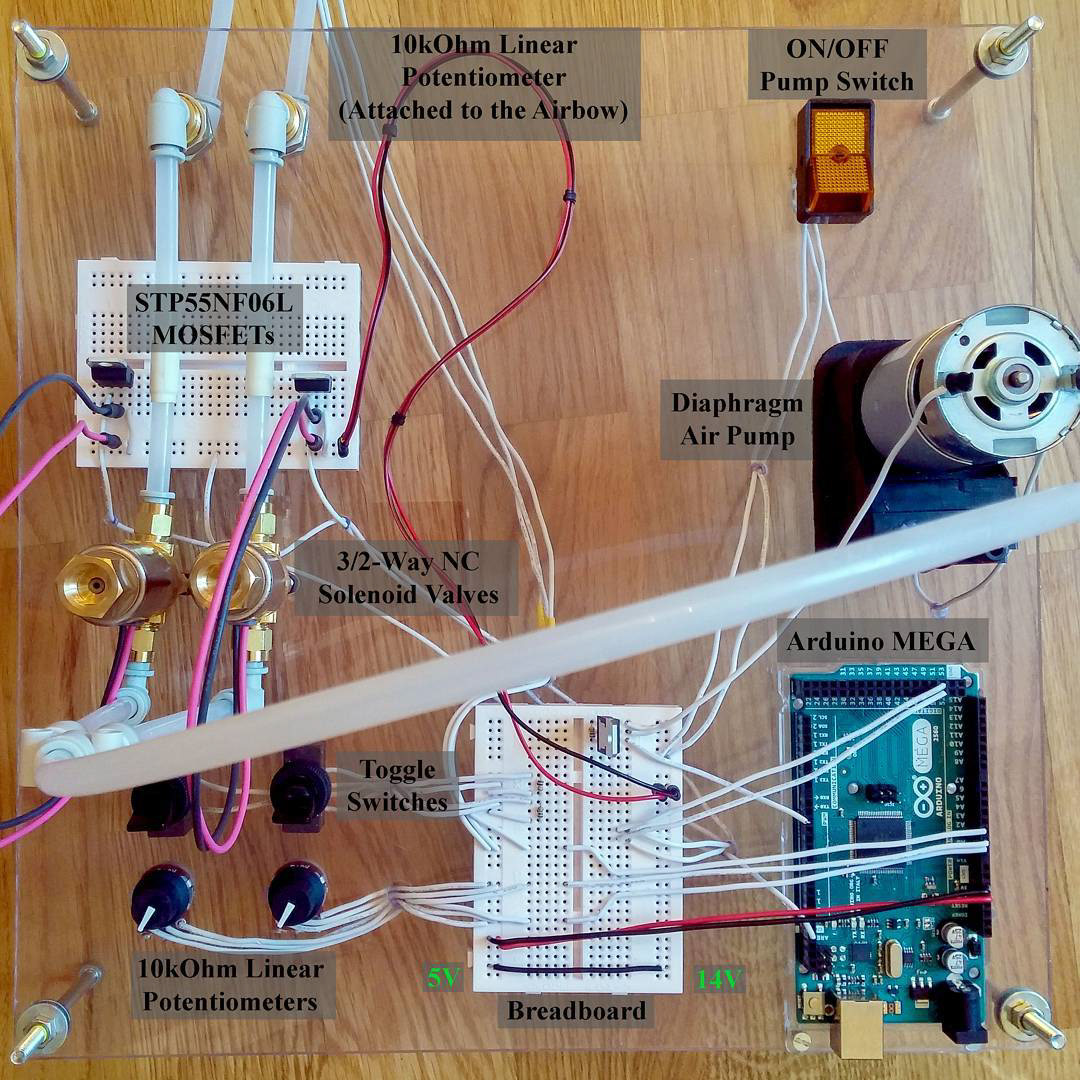
The pneumatic control board that controlled the Airbow. I also wrote the code for the PID controller by myself.
Here I am changing the setpoint via a potentiometer on the control board and monitoring how fast the Airbow adjusts its angle to the new setpoint.
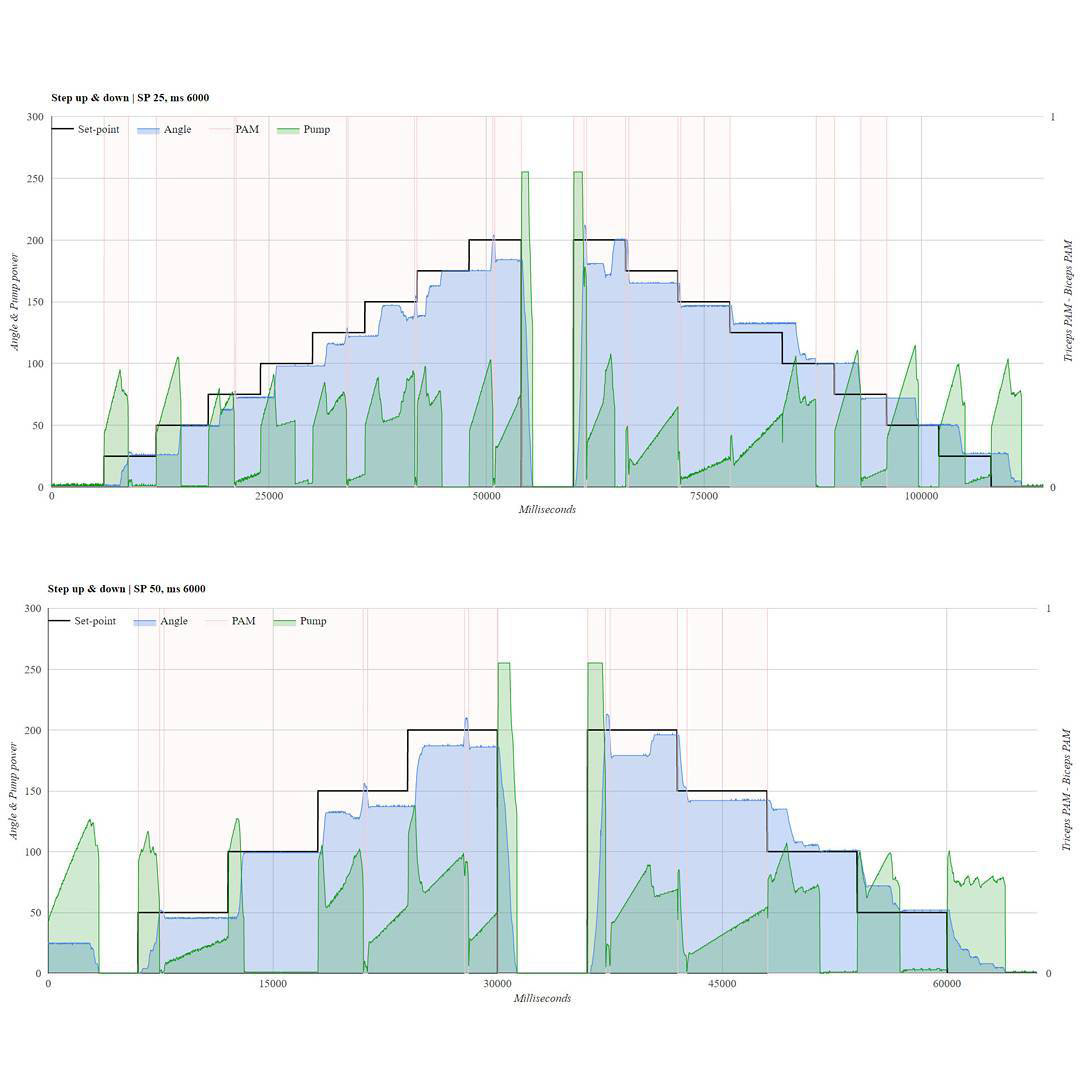
The results from my experiment showed backlash that was caused by too much friction in the joint.